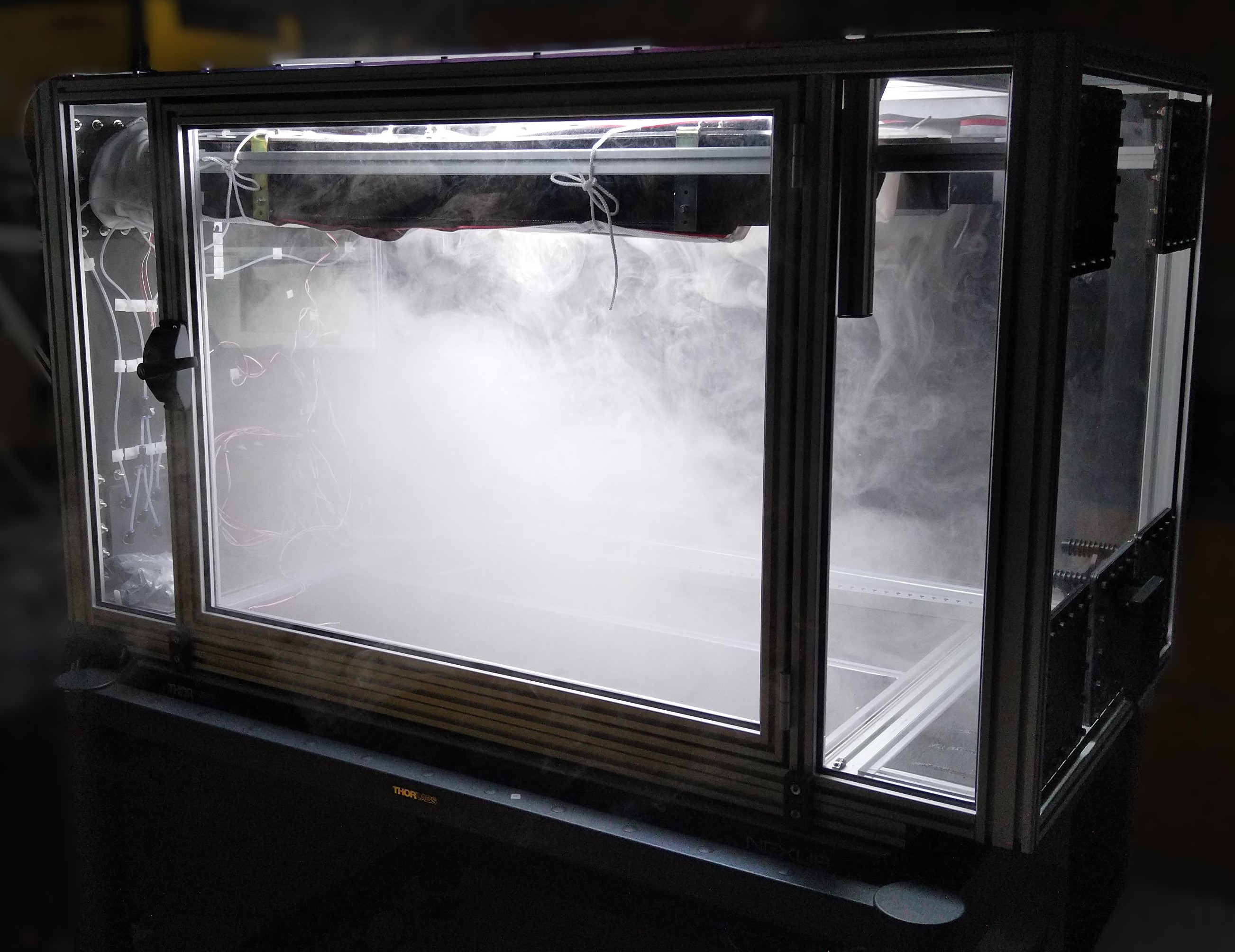
Thermal breadboard for precision interferometry measurement
Various UK Standard for Professional Engineering can be identified through this complex project. Some are related to a pure technical engineering field, while others are linked to soft skills such as decision-making skills, leadership, and management skills as well as personal commitment.
The so-called 1D machine is a new instrument developed within NPL and aims to be a secondary standard calibration system. This instrument is specified to be an all-in-one calibration device, able to provide a traceable link to the primary realisation of the metre, for the lengths of artefacts of various types. These are gauge blocks, length bars, step gauges, and internal & external diameter standards. The ability to measure multiple types of artefacts presents several advantages, including small form factor, process automation, adaptability to customer demands; this new concept also promises a step change in measurement uncertainty. The instrument relies on laser interferometry measurement through air at temperature controlled at or close to 20 °C, along a distance varying from a few millimetres to 2 metres. This interferometric measurement is influenced by the refractive index of air, which for instance would be locally affected by heat from various thermal sources. To overcome these issues, thermoregulation of the optical transit path through enclosed air has been proposed, relying on using multiple air diffusers.
From October 2020, I have taken the lead in developing the temperature-controlled chamber, to reach 10 mK accuracy on a define air volume, at a prototype level (smaller scale), using multiple air diffusers. At that time the concept design lied on a six-page document, completed by a requirement design document. I have analysed the requirement and proposed to design the system in a way to have compatibility between the electronic and the computing software, taking account on ramping up the development of the controller. I have motivated the idea of using mainstream low-cost prototyping electronics (Raspberry Pi and Arduinos) together with the use of Simulink, rather than expensive proprietary systems commonly used across our organisation. To influence this decision, I proposed a development framework which would allow developing both hardware and software in parallel but in an independent manner. I pointed out that Simulink would be the best tool to enable the development of the controller of a system that presents long time constants, and with the capability to transition from a model-based algorithm to embedded machine code with minimal effort.
The prototype incorporates four main stages: the main enclosure, the heat exchangers, and the electronics able to measure the temperature, drive the fans and the heating/cooling devices, and the computing programs, either deployed on microcontrollers (Arduinos) or the Raspberry Pi. These tasks are conducted in parallel.
From November to December 2020, I have pre-designed sized the main enclosure as well as the heat exchangers and their diffusers. This pre-design was a starting point prior to engage talks with potential suppliers, based in the UK and USA. I scheduled various meetings to better understand the capability of the potential partners in delivering bespoke components. I then refined the design and requested quotations prior to purchase. I received the different pre-assembled components around January 2021, and I had to make design adjustment in order to complete the assembly, such as drilling panels, designing 3D printed ducts, soldering connectors on the fans, etc. This task is still evolving as additional subsystems are incorporated to the build.
In parallel of designing and building the mechanical hardware, I am developing the electronics and software. I had to familiarise with the various Integrated Development Environments, and particularly Simulink, to deploy programs on the Raspberry Pi. Through various pre-test I carried out, I identify the limitation of the GPIOs of the computer. If it was originally thought to use a single “target”, I had to change my design and use secondary platforms (Arduinos or integrated circuits) to complement the functionality of the single board computer, such as using dedicated fan drivers integrated circuits, heat exchanger drivers, etc.
From January 2021, I decided to focus on building the individual platforms to communicate with the Raspberry pi using i2c. This guided the design of prototype boards I assembled. For some drivers, I liaised senior electronic engineers so that they could provide a specific design, and I contacted some of our apprentices to manufacture them and test before integration. As part of an iterative process, electronic design had to change.
In April 2021, I found the temperature resolution which could be achieved with the original temperature reader was providing a too low resolution. Therefore, I sourced an alternative integrated circuit. As my workload was increasing, I asked my group leader to get someone involved in assessing this new component. One of our senior engineers joined the project and I delegated the task of evaluating the new chip, understanding its performance and limitations to a senior colleague. This person however did not know much about Arduino framework and microcontroller. During few meetings, we had a read through the datasheet to understand the various mode of operations. She sourced the evaluation board kit which fortunately was using the Arduino framework. I shared my knowledge to the colleague who joined the project, discussed with her the demonstration code in conjunction with the datasheet, and provided some guidance to carry out some digital signal processing (Butterworth filtering) to improve the sensor accuracy. Thanks to her, I could adapt her code for a single sensor to multiple sensors by developing a dedicated Arduino library allowing a non-blocking sequential measurement operation around August 2021.
The development and implementation of a controller for a system that present long time constant (minutes to hours) can be a fastidious task. To enable a faster development, I motivated the idea of using a model-based design approach using Matlab/Simulink. The methodology relies on developing a controller for a plant model which can operate at a faster rate than the physical model. I have motivated the choice of MATLAB/Simulink rather than other software used across our organisation, as it can handle the model-base design and the direct translation to the target, while offering multiple levels of checks for code integrity, controller saturation and stability… The main drawback is the model needs to provide an accurate representation of the physical plant.
For this, I am using two different approaches: system identification and model response of a FE model.
I have made the choice to delegate the FE model to one of my colleagues specialised in numerical modelling. I am actively providing detailed parameters required for the modelling task and reviewing the output of the model to ensure it provides an accurate representation of the physical system.
To prepare the system identification procedure, I have also integrated a messaging MQTT functionality to monitor the sensor and overwrite the controller. This allows a total remote control from the system. I have also implemented a datalogger on the controller hardware, as well as a timeseries database. The system. I am using this messaging system to drive the system with external scripts and assess the time response of the plant at different location.
In parallel of the technical work, from 7th of June to 9th of June 2021, I supervised two 16-year-old school students. As part of their school program, I organized a three-day introduction to engineering works. I involved them in developing a thermal insulation gasket for the cooling bock of the thermal breadboard, from design specification to preliminary hand drawings. I guided them through the whole process, providing some input such has technical documentation from manufacturers (application note, datasheet, compliance document...), risk assessment, health and safety, product cost, lead time, CAD drawing, defining essential requirements of the product, propose concept ideas and compare them together. I provided some demonstrations of the CAD software as well as the Finite Element software I am using.
Since January 2022, an electronic technician has joined our team, and spend her time on improving the electronic of the prototype. I have provided a large overview of the project and specific issues I am facing during its development. As part of this non-formalised mentoring, I am supporting her in both technical aspects and integration within our organisation. On the technical aspect, I am keeping myself available to answer specific questions and give explanations of certain choices that have been made in the past and discuss work progression. Regarding the integration within our organisation, I have introduced her to our team, and I am helping her on daily administrative tasks, such as purchasing, sourcing components, health and safety forms.
Finally, I have presented part of my work at the EUSPEN-SIG conference: Thermal Issue in Zurich 2022. The attendance to the conference was proposed by my line manager who is also working on the project. I suggested that rather than attending the conference, it would be worth to present part of my work. This would enable to publish and formalise some achieve milestones and allow me to expand my visibility as an engineer, within our company but also within the scientific community. Due to some uncertainties related to covid-19, rules of travel and company travel policies, I entered the conference late as a presenter, and I found challenging to write an abstract and prepare a fifteen-minute oral presentation in one week. I could manage my time to deliver and present at the conference. During this conference I could exchange and network with other engineers and researchers working for various organisation, such as CERN, METAS, PTB, Zeiss…
One challenge to attend the conference was the formal travel requests to comply with. Our organisation has setup a triage team to allow foreign travels during the pandemic. I had to get approvals from my department head, write a travel risk assessment, write an emergency response plan in case of covid episode, and book my trip, accommodations via our travel agency.